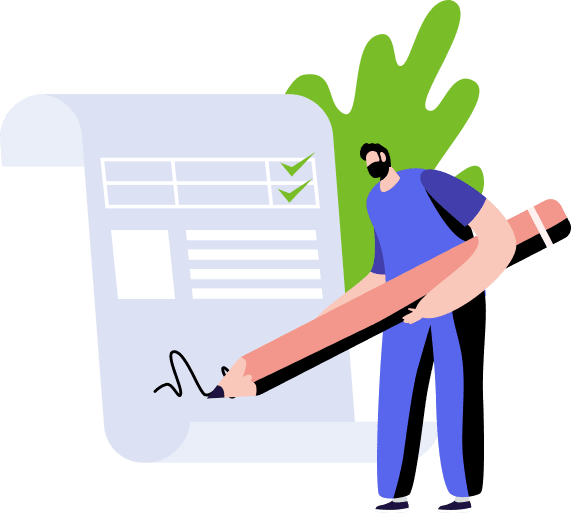
The sum of direct materials cost and direct labor cost is known as prime cost. The failure of trade deficits to balance has many causes, with tariff and non-tariff economic fundamentals as major contributors. Regulatory barriers to American products, environmental reviews, differences in consumption tax rates, compliance hurdles and costs, currency manipulation and undervaluation all serve to deter American goods and keep trade balances distorted.
What are nonmanufacturing overhead costs?
- This calculation assumes that persistent trade deficits are due to a combination of tariff and non-tariff factors that prevent trade from balancing.
- The direct materials would include the metal for the frame, tires, and handlebars.
- That is why accountants refer to nonmanufacturing costs as period costs or period expenses.
- Direct materials usually consists of a significant portion of total manufacturing cost.
- Figure 2.4 shows examples of production activities at Custom Furniture Company for each of the three categories (we continue using this company as an example in Chapter 2).
- Non-manufacturing expenses have no effect on the production cost of the company because they are treated as period costs.
Direct labor – cost of labor expended directly upon the materials to transform them into finished goods. Direct labor refers to salaries and wages of employees who work to convert the raw materials to finished normal balance goods. Things that are resources owned by a company and which have future economic value that can be measured and can be expressed in dollars. Examples include cash, investments, accounts receivable, inventory, supplies, land, buildings, equipment, and vehicles. This account balance or this calculated amount will be matched with the sales amount on the income statement. It is likely that you will have to estimate the cost of these activities.
Purpose of Financial Accounting, Cost Accounting, GAAP, and IFRS
This calculation assumes that persistent trade deficits are due to a combination of tariff and non-tariff factors that prevent trade Retail Accounting from balancing. Examples of general and administrative costs include salaries and bonuses of top executives and the costs of administrative departments, including personnel, accounting, legal, and information technology. “Business in Action 2.5” details the materials, labor, and manufacturing overhead at a company that has been producing boats since 1968. Table 2.2 provides several examples of manufacturing costs at Custom Furniture Company by category.
What are Non-Manufacturing Overhead Costs?
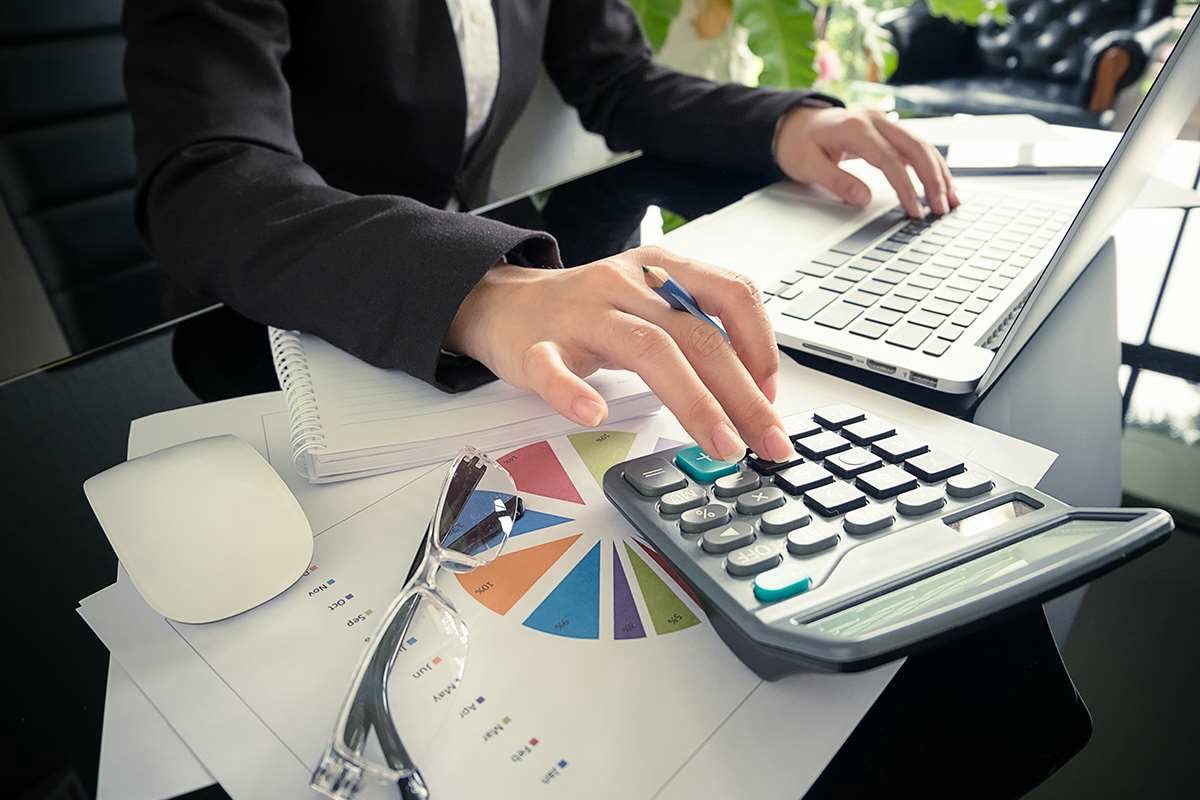
The cost of inventory should include all costs necessary to acquire the items and to get them ready for sale. The systematic allocation of the cost of an asset from the balance sheet to Depreciation Expense on the income statement over the useful life of the asset. (The depreciation journal entry includes a debit to Depreciation Expense and a credit to Accumulated Depreciation, a contra asset account). The purpose is to allocate the cost to expense in order to comply with the matching principle.
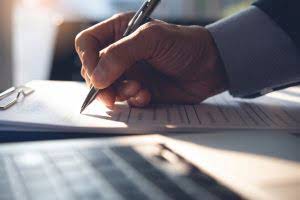
Part of cost of goods sold
Nonmanufacturing overhead costs are the business expenses that are outside of a company’s manufacturing operations. In other words, these costs are not part of a manufacturer’s product cost or its production costs (which are direct materials, direct labor, and manufacturing overhead). Manufacturing costs other than direct materials and direct labor are categorized as manufacturing overhead cost (also known as factory overhead costs). They usually include indirect materials, indirect labor, salary of supervisor, lighting, heat and insurance cost of factory etc.
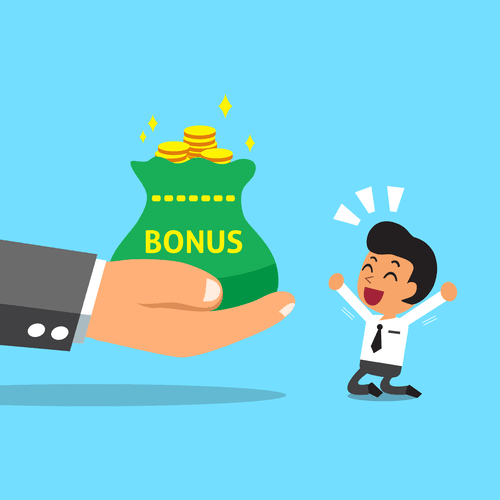
Manufacturing overhead might include the cost of factory utilities, depreciation on manufacturing equipment, and the salaries of factory supervisors. Sometimes it is difficult to discern between manufacturing and non-manufacturing costs. For instance, are the salaries of accountants who manage factory payrolls considered manufacturing or non-manufacturing expenses?
What about the office rent for the vice president of manufacturing? Therefore, businesses typically establish and adhere to their own criteria. Nonmanufacturing overhead costs are the company’s selling, general and administrative (SG&A) expenses plus the company’s interest expense.
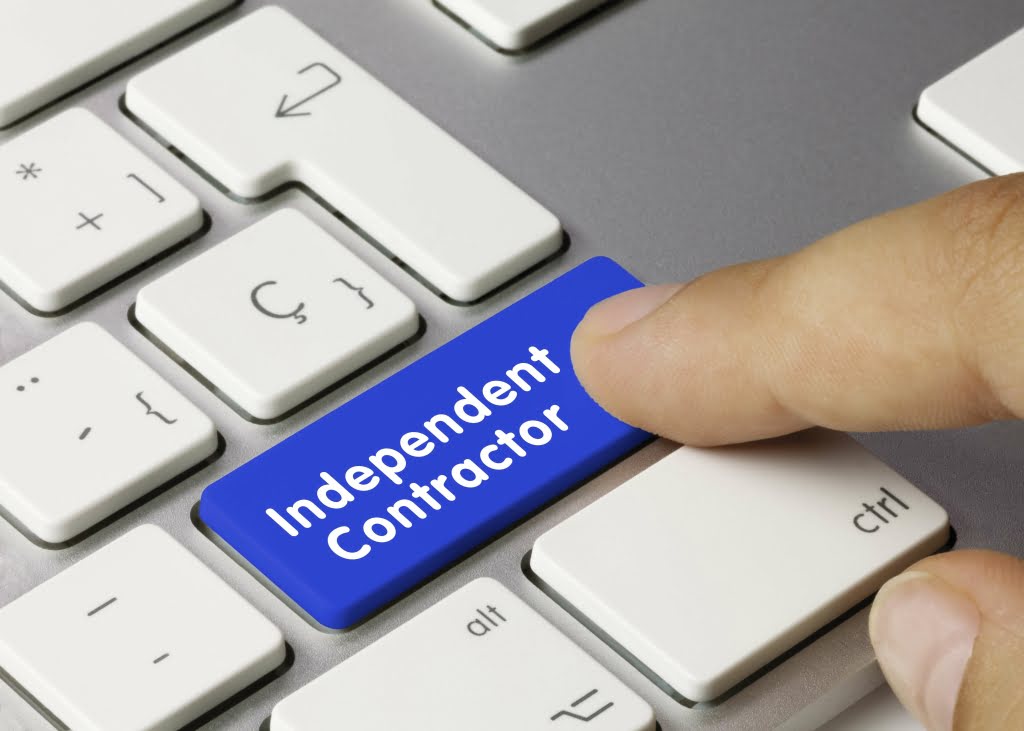
- Costs may be classified as manufacturing costs and non-manufacturing costs.
- Manufacturing and non-manufacturing costs together form total costs for a manufacturing entity.
- Manufacturing costs refer to those that are spent to transform materials into finished goods.
- Thus, management attention must be focused on both the core and the ancillary costs to control and manage them with a view to maximize profitability on long term basis.
- This article looks at meaning of and differences between two main cost categories for a manufacturing entity – manufacturing cost and non-manufacturing cost.
The recent experience with U.S. tariffs on China has demonstrated that tariff passthrough to retail prices was low (Cavallo et al, 2021). Reciprocal tariff rates range from 0 percent to 99 percent, with unweighted and import-weighted averages of 20 percent and 41 percent. This article looks at meaning of and differences between two main nonmanufacturing costs include cost categories for a manufacturing entity – manufacturing cost and non-manufacturing cost.